Process Safety
Improve Operations and Mitigate Risk
Do you know if your process operates at an acceptable risk?
Much depends on the safety layers built into your process operations and company-wide safety strategies and policies. To identify and prevent safety risks and hazards in your facility, it is vital to implement and maintain process safety.
When it comes to process safety projects and hazardous operations, such as startups and shutdowns, MAVERICK Technologies brings deep domain experience, leveraging industry standards and best practices to help increase facility output, improve operational quality and efficiency, ensure safety and enhance regulatory compliance.
To improve operations and prevent incidents, MAVERICK subject-matter experts apply a combination of:
- Process control knowledge
- Industrial automation depth
- Safety Instrumented System (SIS) expertise
To us, it’s not just about the technology and processes, it’s also about the people in your facility. We ensure facility personnel have the right tools and technology required to do their respective jobs. We also help them better understand their role in the broader process safety picture and ensure continuous improvement measures are in place to maintain operations.
The MAVERICK Approach
MAVERICK understands that you must make upfront decisions about your operations, identify risks and how much risk you will tolerate.
Project management is one of the most important factors in the success of a process safety project. MAVERICK employs the Project Complete® approach to project management, which our project managers execute at every stage in the process safety project lifecycle: define, design, develop, deploy, direct, document.
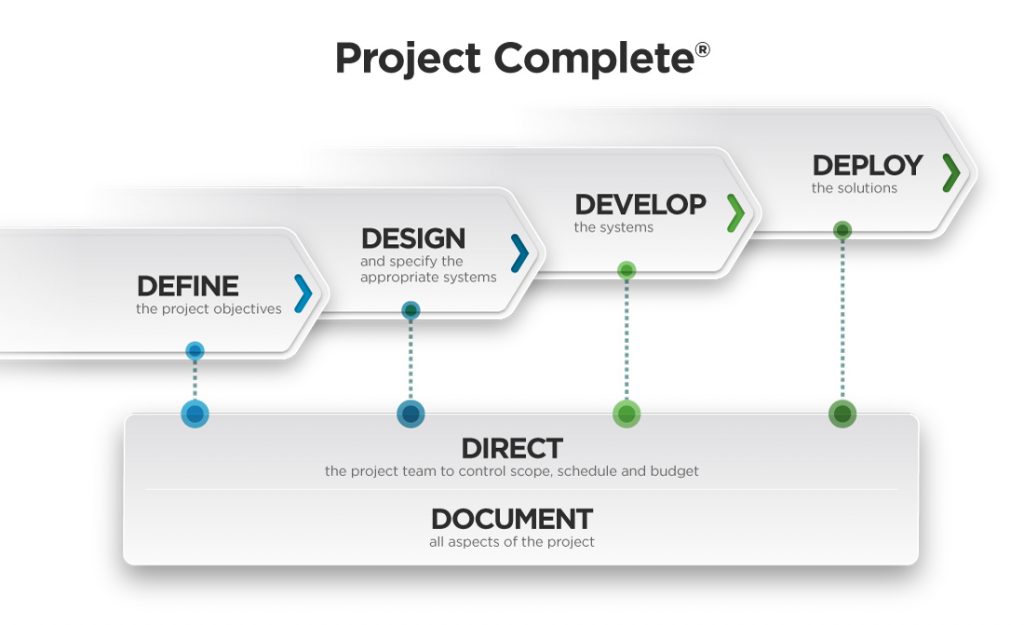
MAVERICK experts can help with your functional specifications, planning and execution.
-
1
Define
-
2
Design
-
3
Develop
-
4
Deploy
Hazard Identification (HAZOP)
Typically referred to as a process hazard analysis (PHA) or HAZOP. It is the step where a facility identifies hazardous scenarios. At a minimum, it requires a trained facilitator, a subject-matter expert from process engineering, and an operations representative. Often the team will be larger and include both internal and external operators/supervisors, as well as other engineering disciplines such as process control, mechanical and electrical.
Layer of Protection Analysis (LOPA)
LOPA is one way to perform process hazard analysis (PHA). It involves analyzing the tolerable risk remaining after safety protections are applied.
Tolerable Risk
Tolerable Risk is the benchmark that a company uses to determine their relative safety strategy. Most large operators have these decisions quantified in tables and charts. If you are starting to implement SIS in your facility, this is a critical step, and we can help with experienced facilitators and experts.
Probability of Failure on Demand (PFD) Calculations
How do you know that the interlock you’ve been relying on is going to meet the criteria for SIL2? You must do the math. We can help guide you through this process.
Installation Details
When installing any new instrument, but especially when implementing a new SIS protection layer, the instrument must be installed right. Our team of experienced designers can provide detailed instrument installation details for your next project.
Software Requirement Specification (SRS) Generation
An SRS is a requirement of the safety standard and specifies all the details of the SIL function. It includes the document that proves the protective function will satisfy the intended use. Whether you have your own template, or want us to use ours, we have the range of disciplines required to complete the specification.
Certified vs Proven in Use
For an instrument to be used in SIL service, it should have a SIL certification from the manufacturer or the operator can self-certify that it is proven in use. We can help you make the decision and setup the record keeping that you will need if you decide to self-certify.
SIL Calculations
Just because a SIL3 transmitter is connected to a SIL3 PLC and it closes a SIL3 valve, the function is not SIL certified. It only means that the components are SIL3 capable. SIL functions must meet their required probability of failure on demand (PFD). To determine the probability of failure on demand (the odds that the system will work when called upon), you must do the math. We have experience analyzing SIL levels using many commercially available software packages.
Proof Test Procedures
Part of the determination of a SIL function is how often it will be tested to try to find undetected faults (i.e., it broke, but you can’t tell). This test is called a proof test. We have written procedures for proof testing instruments, valves, motor contactors and logic solvers.
Validation Procedures
Before a SIL function be considered “in-service,” it must be tested in place, validated. We have written validation procedures for many of our customers, and our field technicians have executed even more.
HMI and Control Programming
In addition to safety system programming, some LOPA-credited protections are implemented as interlocks and alarms on the Basic Process Control System (BPCS). MAVERICK has experience implementing BPCS protections on almost all DCS and PLC systems in industrial use.
SIF Programming
When programming a safety system, it is important to understand the safety manual and best practices for the logic solver. With dedicated technology leaders, MAVERICK has a commitment to quality in all the platforms we support.
Code Verification and Assessment
For a safety system, good programming practices isn’t enough. The control code must be tested to prove functionality, and it must be assessed to prove that the rules of the safety manual were followed.
Commissioning and Field Verification
Once installed in the field, a verification test proves that the safety function will work when needed. MAVERICK’s field technicians have experience executing SIS validations across many industries.

MAVERICK Can Help:
- Initiate or rejuvenate your Process Safety Management (PSM) programs and guidelines.
- Perform a Process Hazard Analysis (PHA)/Hazard and Operability (HAZOP) study or other audit to determine any safety-related issues or to identify those situations or potential system failures that could happen to cause an accident or issue.
- Provide experts with varying backgrounds who can provide insights and information on your facility’s critical systems.
- Review the conclusions from the PHA/HAZOP discussions and ensure that they are applied properly.
- Establish alarms for critical events, and understand the response required for each alarm.
- Facilitate OSHA-mandated training so operators understand all changes to standard operating procedures and can identify potential hazards.